Our technologies
and services
With our combined experience of Promill Stolz and Maguin Promill, we offer a wide range of proven and innovative solutions designed to meet our customers’ requirements.
Our key technologies
Air Heater Technology
For over 15 years, Promill has developed and suppled numerous air heater based on their own, specialized design optimized to operate as energy source for a rotary dryer drying various products of the agro-industry.
For example, Solid Fuel Air Heaters are the perfect hot air generator designed to operate with our dryers based on available, cheap fuel commodity like wood chips, bark.
In addition, based on our experience and expertise supplying several gas fired air heater with our dryer, early 2000 we decided to develop our on Natural Gas Fired Air Heater optimized and design to operate with our rotary dryer burner not only Natural Gas but other gaseous fuels like Bio Gas, Methane.
In addition, we have improved our Natural Gas Fired Air Heater design even further allowing us to burn the non-condensable matters ager our Turbo drying system – Air Heater operating as thermal oxidizer.
Finally, we supply Heavy Fuel Oil Air Heater and Coal Travelling Grates together with our Dryer.
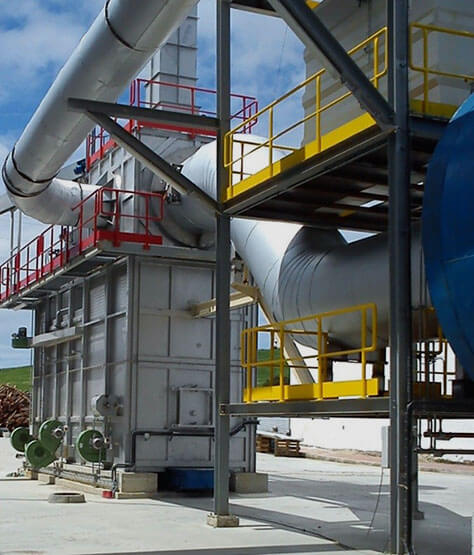
Fields of application
- Beet pulp
- Grass/Alfalfa
- Corn gluten feed
- Wood particles/Sawdust
- Biomass
- Fertilizer
- Fruit by-products, algae, chicken manure
Benefits
- Large dimensioning
- Scaling from 2 to 70 MW (natural gas)
- Scaling from 2 to 25 MW (biomass)
- Low excess of air
- Destruction of VOC by patented natural gas burner
- Solid fuel with wet or dry biomass
- High dilution by recycle or boilers gases
- Elimination (clearing ) of silica/sand/ash before dryer
- Full control of regulation of air flows and fuel feeding linked to the rotary drying loop
- Burner management control and PLC included
- Compliance with NOX and CO regulation
Triple Pass Drum Drying Technology
Promill has a proven experience for 60 years in conception and manufacture of 3 pass dryers for various products and fibres of the agro industry.
The 3 pass drum dryer offers following benefits which results in leading technology in the world.
“Inflight drying” in the passes allows to dry various products with different sizes/granulometries/moisture at different air speeds with a security of homogeneous final moisture and quality.
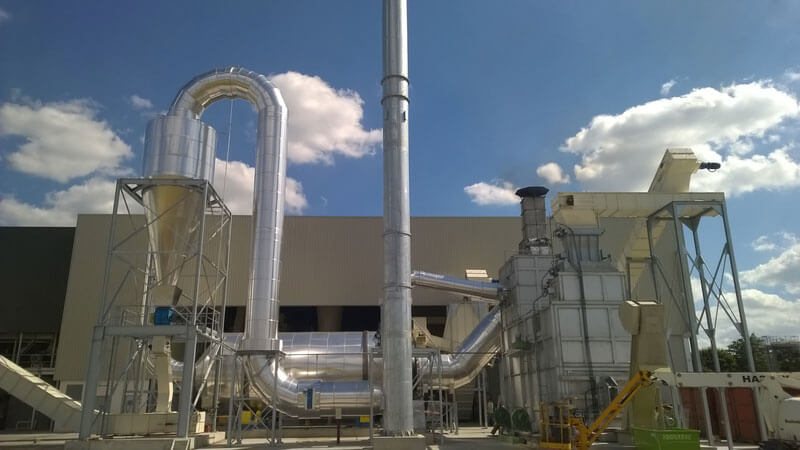
Fields of application
- Beet pulp
- Grass/Alfalfa
- Draffs out of wheat, corn, barley
- Wood particles/Sawdust
- Fruit by-products, algae, chicken manure
Benefits
- High thermal efficiency
- Scaling with 1 drum from 1T to 85T/H evaporation of water
- Very low maintenance cost
- Compliance with various dust and emission regulations
- Compact layout
- Easy control
The turbo indirect dryer
The Promill TURBO indirect drying concept aims at combining the best heat recovery and destruction of VOC (smell).
This is achieved by an integrated recovery of energy to recover more than 80 % of latent heat, resulting in, for example, net thermal requirement of minimum 130 kcal/kg evaporated water and wet bulb temperature of 98°C.
Main features
The turbo indirect drying unit is fitted with well proven equipment:
- The traditional 3 pass drum
- The specifically designed heat exchanger (no product clogging inside tubes)
- Drying in an almost closed loop with offgases vapour at up to 98°C wet bulb
- Maximum energy recovery
- Non condensable vapour is incinerated inside a patented burner resulting in VOC destruction
- Can be combined with a belt drying plant for increasing evaporative capacity
- Easy regulation
- Full security against fire/explosion
Fields of application
- Secondary applications in food processing industry with concern of vapour at over 98°C wet bulb and environmental compliance
Single Pass Drum Drying Technology
Promill has a proven experience for 60 years in conception and manufacture of single pass dryers for DDGS, corn gluten feed and heavy density products.
Single pass design is also proven in wood industry for Oriented Strand Boards (OSB).
The single pass drum dryer offers following benefits which results in leading technology in the world.
Fields of application
- DDGS out of wheat, corn, barley, corn gluten feed
- Wood particles for OSB
- Fruit by-products, algae, chicken manure
Benefits
- High thermal efficiency
- Scaling with 1 drum from 1T to 40T/H evaporation of water
- Very low maintenance cost
- Compliance with various dust and emission regulations
- Compact layout
- Easy transport to site
- Easy assembly and construction on site
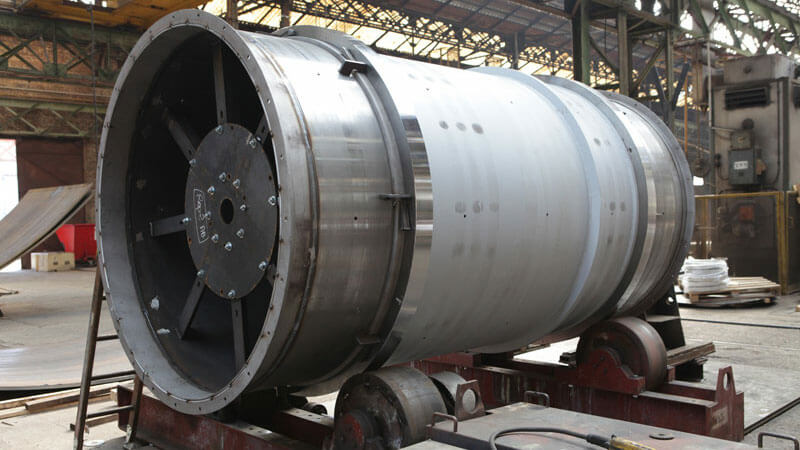
The turbo indirect dryer
The Promill TURBO indirect drying concept aims at combining the best heat recovery and destruction of VOC (smell).
This is achieved by an integrated recovery of energy to recover more than 80 % of latent heat, resulting in, for example, net thermal requirement of minimum 130 kcal/kg evaporated water and wet bulb temperature of 98°C.
Main features
The turbo drying unit is fitted with well proven equipment:
- The traditional single pass drum
- The specifically designed heat exchanger (no product clogging inside tubes)
- Drying in an almost closed loop with offgases vapour at up to 98°C wet bulb
- Maximum energy recovery
- Non-condensable vapour is incinerated inside a patented burner resulting in VOC destruction
- Can be combined with a belt drying plant for increasing evaporative capacity
- Easy regulation
- Full security against fire/explosion
Fields of application
- DDGS
- Secondary applications in food processing industry with concern of vapour at over 98°C wet bulb and environmental compliance
Belt Drying Technology
Since 1997, Promill has designed and supplied numerous belt dryers for various products of the agro-industry.
The concept of a belt dryer is to recover low grade energy (hot water, condensates, low pressure steam, condensation of off gases of existing drum drying unit) for drying or pre drying wet products.
This technology can be proposed:
- Either to increase existing drying facility without extra thermal expense
- Or decrease the overall thermal expense of the drying facility
- Or producing an even moisture content of wet product before the drum dryer or the boiler
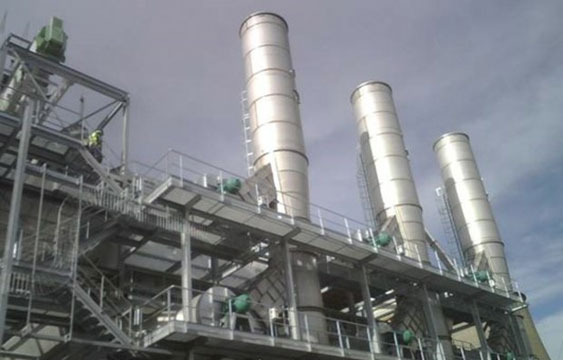
Fields of application
- Beet pulp
- Grass/Alfalfa
- Corn gluten feed
- Wood particles/Sawdust
- Biomass
- Fruit by-products, algae, chicken manure
Benefits
- Strong and robust conception for heavy duty during 8000 hours/year
- High thermal efficiency
- Scaling by prefabricated modules
- Easy transport to site of modules
- Easy and quick installation at site
- Soft regulation
- Very low cost of maintenance
- Compliance with dust regulation
Hammer Mills
The principle of the mills is to reduce the dimensions of incoming materials to a particle size sought after by the mechanical action of hammers coming into contact with the material.
The material thus reduced is conveyed through calibrated screens until the next step of the transformation process.
PROMILL has a wide range of hammer mills to offer solutions to all industries and customers.
The design of the PROMILL hammer mills guarantees the required quality and capacity while optimizing the durability of the components.
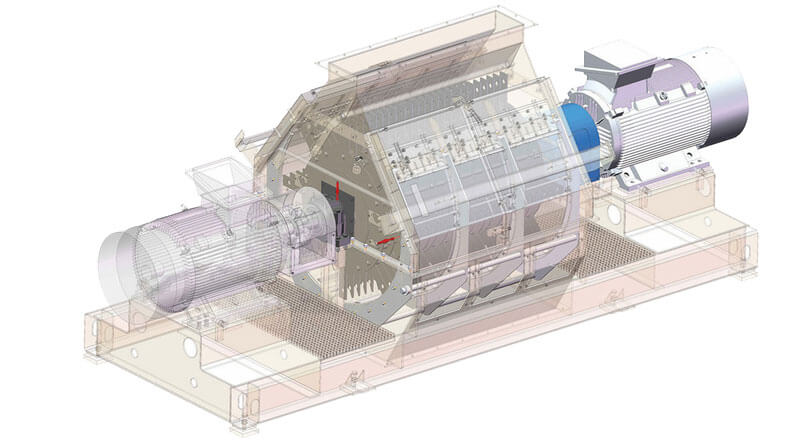
WCR wet hammer mill
This type of grinder is mainly used for the wood industry and for the grinding of plant materials in the post-drying phase.
The moisture content in the material to be crushed is quite high and therefore requires a better grinding torque and an increased strength of the components.
Different powers of motorization are available according to the capacities to be reached.
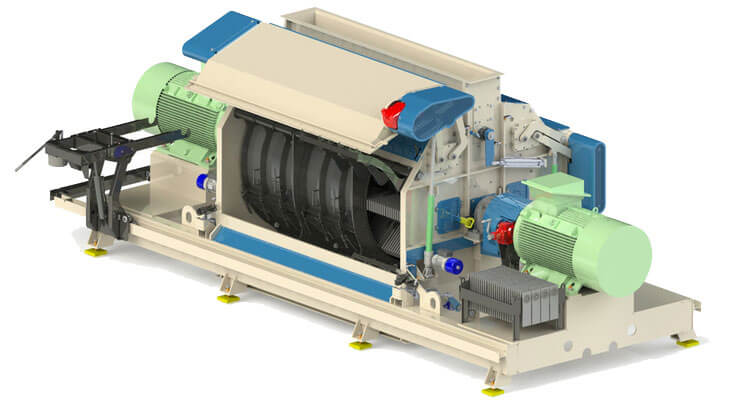
Main features
- Strong build body
- Strong built rotor
- Special reinforced hammers
- High production capacity
- Low energy consumption
Fields of application
- Grinding of wood
- Grinding of DDGS
- Grinding of cereals
Hammer mill refiner type BNA
The BNA mill is used to carry out the final step of reduction of the particles sizes also called “refining”.
The incoming material was previously dried to contain only 8-12% moisture.
The desired particle size is obtained at the outlet of the sizing screens.
Different crusher / refiner sizes are available depending on the materials and production capacities to be produced.
Different powers of motorization are available according to the capacities to be reached.
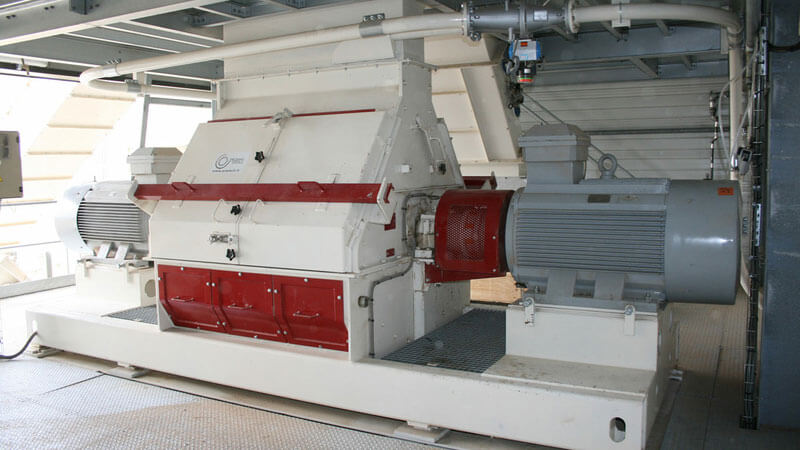
Main features
- Heavy build body
- High capacity low energy consumption
- Flexibility to process many wood species
- Several types of hammers available
- Several screens sizes available
Fields of application
- Grinding of wood
- Grinding of alfalfa
- Grinding of DDGS
- Grinding of cereal products
ROTOMILL Straw Chopper
This equipment has been designed for the pre-grinding of straws used in various applications such as animal feed, litter, biofuels, boiler feed.
Depending on the destination of the finished product the ROTOMILL can be accompanied by a refiner and a pelleting press.
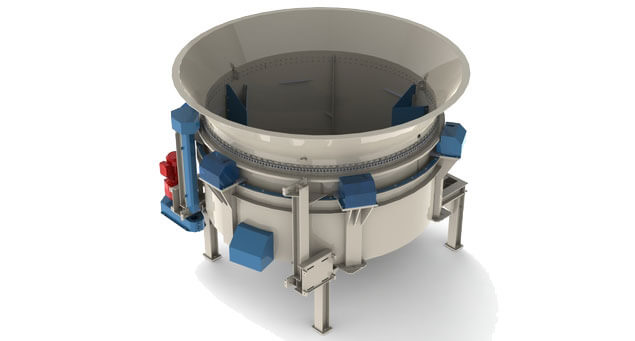
Main features
- Heavy duty equipment
- Capable to process all kinds of straw
- Safety cover
- Inlet filtering device
Fields of application
- Grinding of straw to produce litter
- Grinding of straw to produce animal feed
- Grinding of straw to produce biomass energy
- Grinding of straw to produce biofuels
Bulk grinding Mill type BNE
Different uses are made of rendering products.
BNE grinders have been developed to handle all types of complex materials requiring high abrasion resistance.
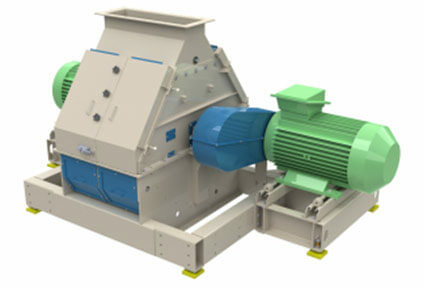
Main features
- Strong build body
- Strong built rotor
- Special reinforced hammers
- Special reinforced counter hammers
Fields of application
- Grinding for rendering of animal products
Pellet mills EVOLUTION series 800 – 900
The robustness and flexibility of the 800 – 900 series makes this range of presses an efficient tool for the production of pellets from a multitude of raw materials and especially materials that are particularly difficult to work with.
Several hundred presses have been installed in the world with success making PROMILL a recognized leader.
Main features
- Unique robustness to work hard and varied materials such as the multitude of wood species
- Patented system of fixing the die ensuring:
- An optimal concentricity of the components in rotation thus limiting the vibrations
- Greater durability of mechanical components to reduce maintenance costs
- The speed and ease of change of the die
- Slow die rotation feature making possible to carry out the positioning adjustment of the rollers in complete safety for the operator
- Instruments for measuring vibration and temperature on bearings and rollers avoiding jamming
- Toothed belt transmission ensuring precision, efficiency, durability and reducing maintenance costs.
- Grease consumption reduction device allowing to make considerable savings.
- Multiple length reduction knives for wood activity
- Automatic adjustment of the position of the rollers for animal feed
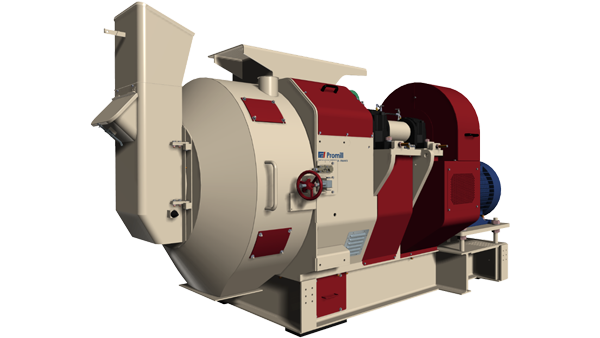
Fields of application
- Pelleting of many different species of wood
- Pelleting of compound feed
- Pelleting of beet pulp
- Pelleting of alfalfa
- Pelleting of DDGS
- Pelleting of cereals
- Pelleting of animal manure
Pellet mills series 2000
This pellet mill series is suitable for high flow pelleting.
The production capacities of this range are perfectly matched to the need for pelleting of various materials intended for animal feed, with a larger diameter die and a higher power motor.
It is the fruit of research and development in partnership with our customers.
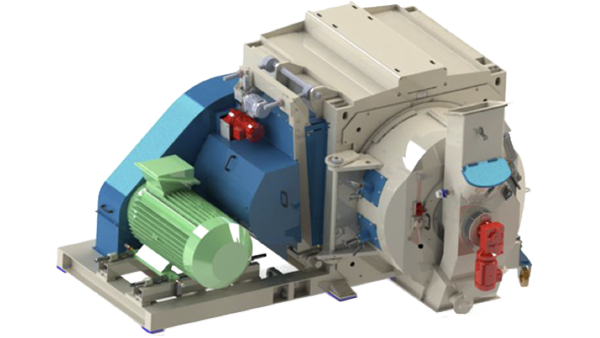
Main features
- Robust design
- High flexibility to process recipes
- Patented system of fixing the die ensuring:
- An optimal concentricity of the components in rotation thus limiting the vibrations
- Greater durability of mechanical components to reduce maintenance costs
- The speed and ease of change of the die
- Slow die rotation feature making possible to carry out the positioning adjustment of the rollers in complete safety for the operator
- Instruments for measuring vibration and temperature on bearings and rollers avoiding jamming
- Toothed belt transmission ensuring precision, efficiency, durability and reducing maintenance costs.
- Grease consumption reduction device allowing to make considerable savings
- Adjustable length reduction knives
- Automatic adjustment of the position of the rollers to save time on recipes change
Fields of application
- Pelleting of compound feed
- Pelleting of DDGS
- Pelleting of cereals
Ancillary pelleting equipment
Pellets Lines
A drying, grinding and pelleting line may be composed of various equipment constituting the chain from the arrival of the raw material to its pre-shipment packaging.
PROMILL manufactures and supplies all equipment necessary to carry out the various steps of the process.
We collaborate regularly with integrators and / or engineering companies that include our equipment in the complete granulation process.
The main equipment is:
- Stone separator: used to evacuate stones, metal parts in front of the hammer mills.
- WCR wet hammer mill: unit designed to crush wood chips having high humidity content.
- Drum dryer: triple pass drying technology allowing to reduce the moisture content of the wood shavings
- Feeding systems: Single feed screw, double regulated feed screw, material storage hopper, mixer, conditioner, many solutions are available to allow an optimal loading of the material to the mills and presses.
- Coolers: At the press outlet, the temperature of the granules is around 80 ° C. It is necessary to cool them to increase their rigidity and to avoid the generation of moisture in their packaging. PROMILL provides different models of horizontal, vertical and countercurrent coolers adapted to the needs of each customer.
- Sifters: To prevent dust from the production of pellets in packaging, we offer a range of rotary or vibratory sieves to remove sieving fines and recycle them. The design of the PROMILL hammer mills guarantees the required quality and capacity while optimizing the durability of the components.
Main features
- Wet Hammer mill reducing high moisture content wood chips
- Drum dryer triple pass with high thermal efficiency
- Dry hammer mill high capacity low energy consumption
- High quality conditioner with injection or water or steam
- Heavy duty pellet mills with low maintenance costs
- High efficiency coolers
- High capacity sifters
Fields of application
- Grinding and pelleting of many different species of wood
- Pelleting of compound feed
- Pelleting of beet pulp
- Grinding and pelleting of alfalfa
- Grinding and pelleting of DDGS
- Grinding and pelleting of cereal products
- Pelleting of animal droppings
- Grinding of material from rendering